Container gantry cranes play a crucial role in the efficient movement of cargo in ports and logistics hubs, ensuring the smooth operation of container terminals. Proper maintenance of these heavy-duty machines is essential to ensure safety, reliability, and longevity. Regular upkeep not only minimizes downtime but also enhances the overall efficiency of container handling operations. H

ere are five essential tips for maintaining container gantry cranes:
Implement a Regular Inspection Schedule
Regular inspections are the cornerstone of effective maintenance for container gantry cranes. Establishing a comprehensive inspection schedule is essential for identifying potential issues before they escalate into major problems. Inspections should cover various components, including the hoisting system, trolley mechanism, rails, wheels, electrical systems, and safety features. Focus on inspecting load-bearing components, connections, and lubrication points. A proactive approach to inspections helps in detecting wear and tear, corrosion, or any anomalies that may impact the crane’s performance.
Prioritize Lubrication and Greasing
Lubrication is crucial for the smooth operation of the moving parts in a container gantry crane. Regularly lubricate critical components such as bearings, gears, cables, and pulleys to reduce friction and prevent premature wear. Establish a systematic greasing schedule, taking into consideration the type of lubricant required for each component. Adequate lubrication not only extends the lifespan of crucial components but also enhances the crane’s overall performance by ensuring smooth and efficient movement.
Monitor Electrical Systems and Controls
Container gantry cranes rely heavily on electrical systems and controls for their operation. Regularly monitor and inspect the electrical components, including cables, connectors, and control panels. Look for signs of wear, corrosion, or loose connections. Implement a comprehensive testing program for electrical systems to ensure that all safety features, limit switches, and emergency stop systems are functioning correctly. Address any electrical issues promptly to prevent malfunctions that could compromise safety and operational efficiency.
Address Corrosion and Paint Maintenance
Container gantry cranes are often exposed to harsh environmental conditions, including salt air in coastal areas, which can accelerate corrosion. Regularly inspect the structural components for signs of rust and corrosion. Implement a robust paint maintenance program to protect the crane’s metal surfaces from the corrosive effects of the environment. Any detected corrosion should be promptly addressed, involving thorough cleaning, treatment, and repainting. A proactive approach to corrosion prevention not only extends the crane’s lifespan but also contributes to maintaining its structural integrity.
Invest in Staff Training and Safety Protocols
A well-maintained container gantry crane is only as effective as the personnel operating and maintaining it. Investing in staff training is crucial for ensuring that operators and maintenance personnel are equipped with the knowledge and skills to handle the equipment safely and efficiently. Provide regular training sessions on crane operation, safety protocols, and emergency procedures. Encourage a culture of reporting any observed issues promptly, fostering a proactive approach to maintenance and safety. Well-trained personnel contribute to the overall effectiveness of the maintenance program and play a pivotal role in preventing accidents and downtime.
Maintaining container gantry cranes is a multifaceted process that requires a combination of proactive inspections, systematic lubrication, electrical system monitoring, corrosion prevention, and staff training. By implementing these five essential tips, operators and maintenance teams can contribute to the longevity, safety, and optimal performance of container gantry cranes. Regular maintenance not only minimizes downtime and repair costs but also ensures that these critical components of the logistics chain operate seamlessly, supporting the efficient flow of goods in ports and container terminals.
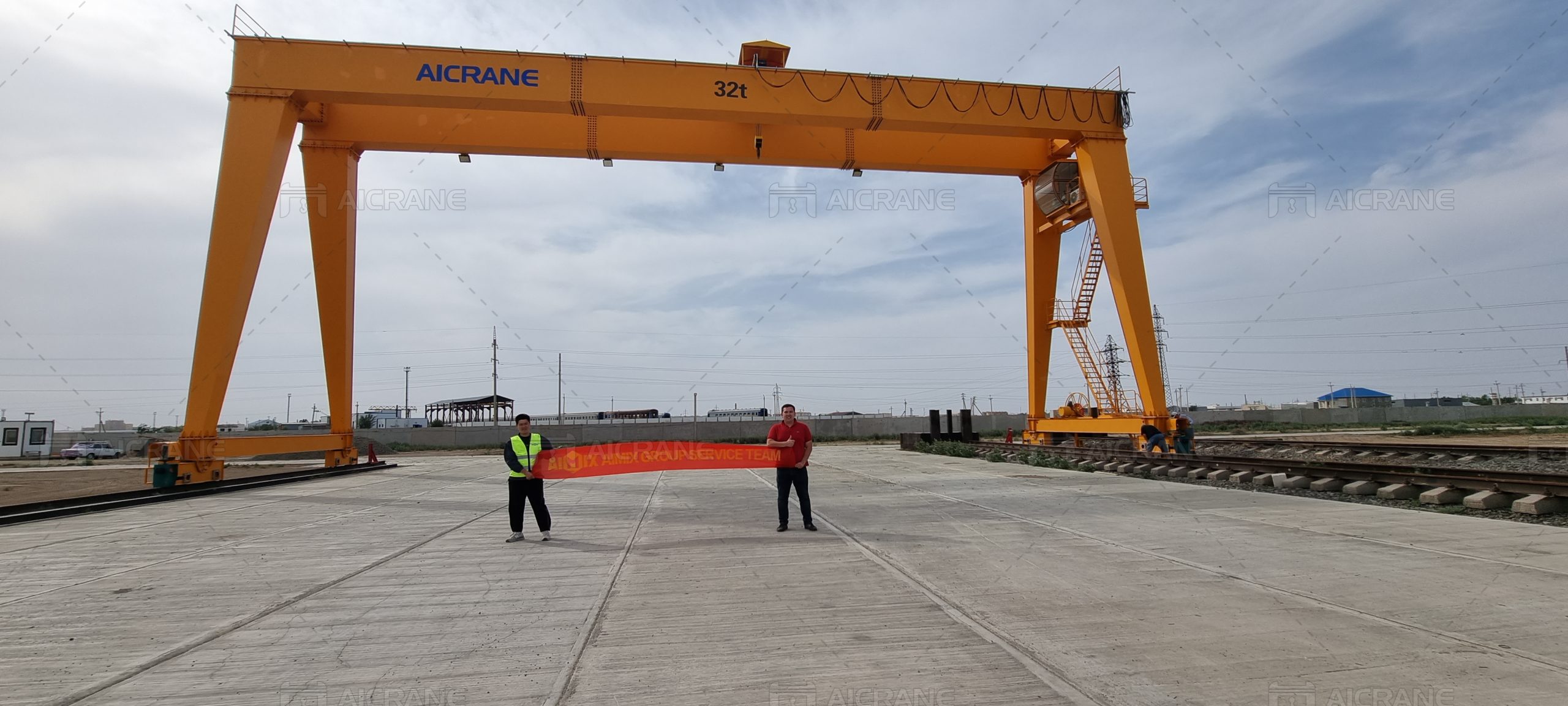
Comments
No comments yet. Be the first to react!